the stationary steam engine.
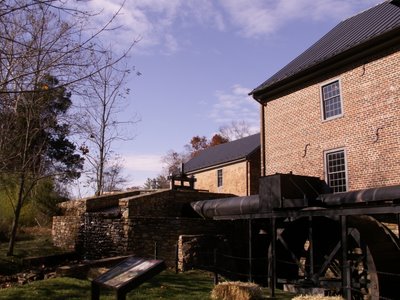
The Aldie Mill was constructed in the early 1800s, and was soon followed by a town bearing the name of Aldie Virginia. The mill would buy local grain crops and grind them into meal and flour, or grind grain for the farmer himself for a fee (which was usually a percentage of the grain.) Since the area relied heavily upon agriculture, the mill eventually became quite a success. So successful in fact that it did not close until 1971 after being owned by six generations of Moore family.
What makes this mill a little unusual is the waterwheel, or rather, waterwheels.
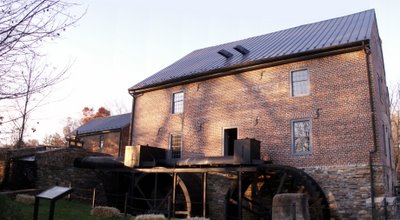
Unlike many mills, this one had two waterwheels instead of just one. This gave the miller more power at his disposal. At one point the mill was operating 5 grist mills at the same time. But before I get too far ahead of myself let's take a moment to look at the process from the beginning.
When you want to use a waterwheel what's the first thing you need? Water of course.

This mill pond has been consructed along the course of a small waterway, so that a sizable quantity of water can be stored.
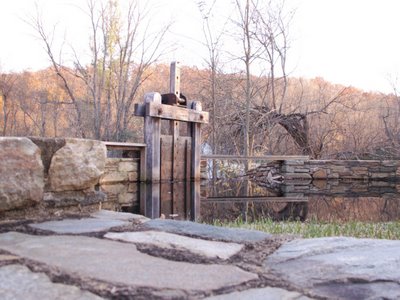
A wooden gate limits the flow of the water so that the mill can be shut off. In this case the gate is mostly hidden because the pond is full and running over the stone spillway. From there, the water flows down a pipe to one of two control gates which allow individual control over each wheel. I suspect these are more recent than the mill itself, but they still aren't new.
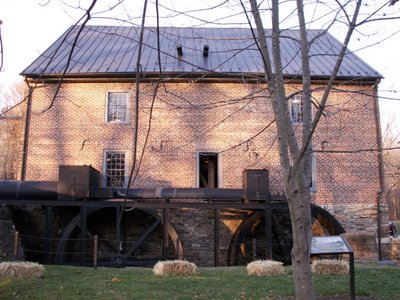
Inside the mill, the miller opens the control gates to start the waterwheels. These monsters (approximately 18' in diameter) are so heavy that it's necessary to fill 3 of the troughs before you see any rotation. A large shaft runs through the wall of the mill, connecting the waterwheel to one of the large gears inside which turns a gear on the shaft connected to one of the mill stones.
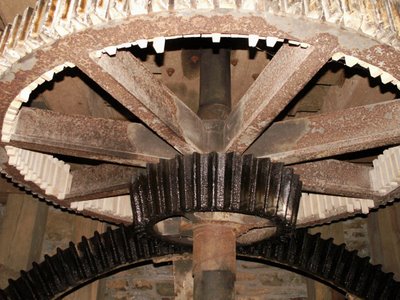
These gears probably replaced a system of wooden cogs with a similar configuration.
Up above that last picture you will find this, the center of activity.
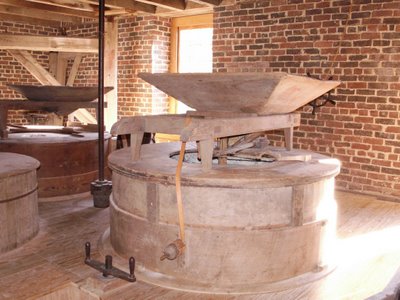
Here, the miller would load grain into the hoppers, either manually from sacks, or by use of the mills built in elevator system, which was capable of conveying grain between all three floors of the mill. The mill would be fed through a hole in the center of the upper stone, and then crushed between the two stones.

This was accomplished by means of multiple grooves cut into the face of the stones. These grooves create a scissors like action which actually cuts the grains. Typically these grooves can also be shaped to limit the travel of the grist so that the smaller particles travel toward the outer edge of the stones. In this case, the stones were quarried in France and shipped, in multiple pieces) the the united states where they were assembled and held together by a large iron band.
The fine particles which escape from the stones, now meal or flower, are funneled down into the basement where they can again be conveyed upstairs. When the grinding is complete, the flour or meal is then conveyed through this hollow beam to the granary next door for storage and sale.
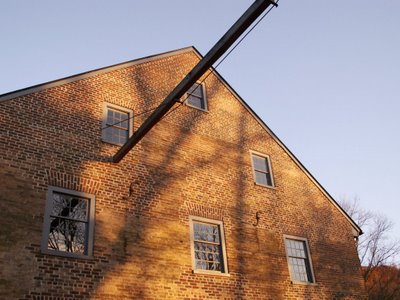
One of the fascinating things about this mill is that it has, at some point, been refitted with newer equipment. So far, the equipment has been directly driven from shafts and gears. A line shaft type system was also used.

Here you can see the input from the other waterwheel, which is conveyed, by a set of gears to the large pulley seen peaking out of the hole in the floor in the phot below.
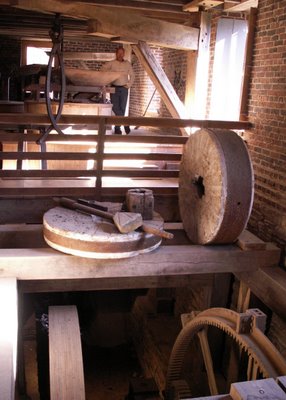
That pulley would have a large belt on it which would be used to turn another, smaler pulley. The smaller pulley would be connected to a large shaft or set of shafts with multiple pulleys and belts for running various machines around the mill. In later years, this would have served a set of roller style mills similar to these.
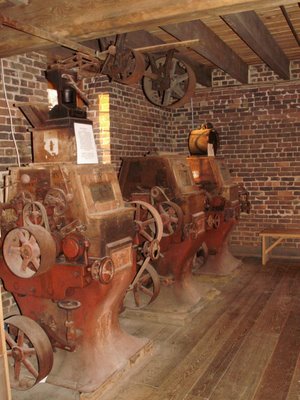
These roller mills provided a more efficient system of grinding because rather than using large, heavy rotating parts to grind the meal all at once, the roller mills use small, high speed rollers to cut and crush the grain. This is done in multiple stages rather than trying to do the work all at once as was the case with stone grinding.
The Aldie Mill eventually succumbed to the ravages of time. For a while it was kept running by using a tractor to drive the line shaft system, but it would have been impractical to continue running the equipment in such a manner. The site has now been restored so that the mill is partially functional.
It is open on the weekends for tours, and occasionally it is run for the enjoyment of the visitors.
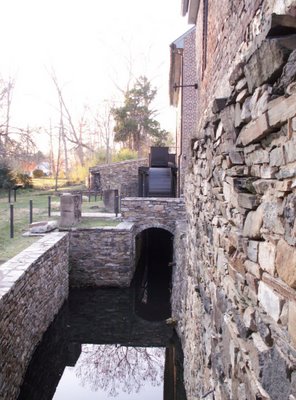
1 comment:
Millers had to be very discreet. Moonshiners require their service to crack the malted (sprouted and dried) corn used to make mash, and of course, the miller could not take his toll from malted corn. He had to remember how much grain was cracked for the moonshner, and then take the toll from the next batch of corn brought in for corn meal. This process occurred in mills all over the country, and ended only after WW2, when independent grist mills disappeared. I have never heard of a miller ratting out a moonshiner.
Post a Comment